Assignment of crash analysis
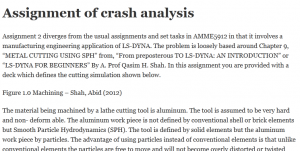
Assignment 2 diverges from the usual assignments and set tasks in AMME5912 in that it involves a manufacturing engineering application of LS-DYNA. The problem is loosely based around Chapter 9, “METAL CUTTING USING SPH” from, “From preposterous TO LS-DYNA: AN INTRODUCTION” or “LS-DYNA FOR BEGINNERS” By A. Prof Qasim H. Shah. In this assignment you are provided with a deck which defines the cutting simulation shown below.
Figure 1.0 Machining – Shah, Abid (2012)
The material being machined by a lathe cutting tool is aluminum. The tool is assumed to be very hard and non- deform able. The aluminum work piece is not defined by conventional shell or brick elements but Smooth Particle Hydrodynamics (SPH). The tool is defined by solid elements but the aluminum work piece by particles. The advantage of using particles instead of conventional elements is that unlike conventional elements the particles are free to move and will not become overly distorted or twisted within themselves. The possibility of negative volume or hourglass errors is also removed. This method lends itself to the modelling of brittle materials like cast iron.
Key Requirements in your Assignment;
1. Read the deck into Presys. The deck is extremely large and is best initially examined using PreSys.
Notepad is not really able to cope with the size. You may like to install Notepad ++ on your own computer. Notepad++ is available from https://notepad-plus-plus.org/download/v7.5.6.html
2. Replace the material being machined in accordance with the table below. Any machinable grade of the
material is acceptable. You will need to research the material properties for your allocated the material according to the last digit of your SID from the table below.
Material Last Digit of SID Cast iron if the sum of last digit of each group member’s SID is 0 or 1 Titanium if the sum of last digit of each group member’s SID is 2 or 3 Aluminium if the sum of last digit of each group member’s SID is 4 or 5 Magnesium if the sum of last digit of each group member’s SID is 6 or 7 Brass if the sum of last digit of each group member’s SID is 8 or 9
e.g. 310275433_307111228_306432899; 3 + 8 + 9 = 20; 0 = Cast Iron
Replace the material (*MAT_020 / *MAT_RIGID) of the tool that is being used with a suitable tool steel.
3. Increase the speed of the cutter in 25% steps until the tool is double its original speed. Comment on each result using post processing methods by referring to database files generated or the ‘PreSys Post Processing Training Manual’ located in the Help > Manual and Tutorial section of Presys.
4. Qualitatively discuss, what is the shape and size of the swarf? Is the material failure worse or better at the
end of the operation as the speed is increased or the depth of cut is increased?
5. Is there an ideal point where material failure is minimised?
6. Your report should be similar to what a junior engineer may produce in their first year of work. The following key points should be included; a. An introduction. b. A contents page. c. Discussion at key steps with comments that describe what the outcomes are. d. Good graphics which are labelled and referenced within your report. e. An in depth conclusion which provides the reader with a broad summary of your work with your final
recommendations on the cutter position and speed to minimise the material failure. f. References used using either the APA 6th or Harvard referencing system..
The report must be in colour and in pdf format. Submit your report and final .dyn, message file and one .avi file through the Assignment section of CANVAS as one file in a compressed format named with all of your group member’s SID as part of the file name e.g.
310275433_307111228_306432899.zip
THIS ASSIGNMENT SHOULD TAKE AN AVERAGE GROUP OF STUDENTS 8 HOURS TO
COMPLETE
AMME 5912 Assignment 2 Marking Sheet 2018
2. Research appropriate materials in accordance with SID. 0 No attempt, 1.5 Basic discussion and attempt at usage of researched material, 3. Comprehensive discussion & σ/ε graph and refs.
/3 3. Increase of cutter speed by 25% steps until original speed is doubled.
0 No attempt, 4.5 Basic attempt with limited discussion, 9. Well documented graphics with clear discussion.
/9 4. Qualitative discussion on the size and shape of the swarf.
0 No attempt, 1.5 Basic attempt with limited discussion, 3. Well documented graphics with clear discussion.
/3 4. Comment on the ideal point where material failure is minimised.
0 No attempt, 1.5 Some attempt with limited discussion, 3. Well documented attempt with clear discussion.
/3 6. Overall Impression
0 No attempt, 0.5 an average attempt with limited discussion, 1 A good submission that is clear and provides comments and demonstrates some level of structure, 2 An excellent submission that is well presented and considers an introduction, contents page, discussion at all key points, relevant graphics, appropriate conclusions and references.
/2
TOTAL /20
TOTAL /15 Marker __________________________
- AMME5912 Assignment 2 2018
- Assignment 2 diverges from the usual assignments and set tasks in AMME5912 in that it involves a manufacturing engineering application of LS-DYNA. The problem is loosely based around Chapter 9, “METAL CUTTING USING SPH” from, “From LS-PREPOST TO LS-DY…
- In this assignment you are provided with a deck which defines the cutting simulation shown below.
- 2. Replace the material being machined in accordance with the table below. Any machinable grade of the material is acceptable. You will need to research the material properties for your allocated the material according to the last digit of your SID fr…
- Replace the material (*MAT_020 / *MAT_RIGID) of the tool that is being used with a suitable tool steel.
- 3. Increase the speed of the cutter in 25% steps until the tool is double its original speed. Comment on each result using post processing methods by referring to database files generated or the ‘PreSys Post Processing Training Manual’ located in the …
- 4. Qualitatively discuss, what is the shape and size of the swarf? Is the material failure worse or better at the end of the operation as the speed is increased or the depth of cut is increased?